Fully automatic saw with optional workpiece
length measurement
Products
In addition to the basic processes of sawing and shearing of tubes and solid material, for example, RATTUNDE production systems can also integrate a wide variety of processes including brush-deburring, end machining, (facing and chamfering of workpieces), and curve machining (thread and groove cutting, drilling, external lathing, external and internal contour lathing and chamfering). In short, you’ll have a high-performance system tailored specifically to your requirements, the corresponding service, and finished end products that are labeled, measured, washed and stacked, ready for you to pack and ship.
All-in-one solutions
RATTUNDE Services at a Glance


Sawing and chamfering machine for the single cut.
Efficient production right from the start!
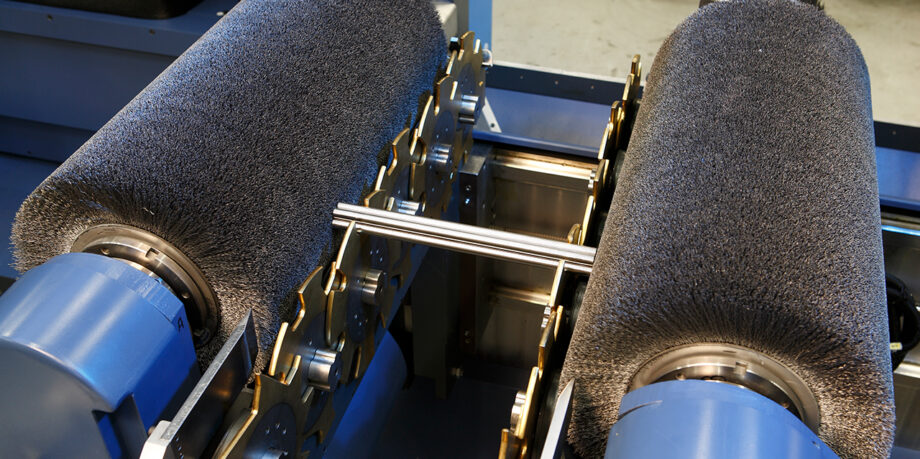
A concept
for sawing and deburring
for single and multiple cut applications

Combined processing unit
- sawing machine,
chamfering system and integrated deburring machine

Precision system for complex processing
of tubes and solid material.
Cutting and end-machining

TWINCUT
Sawing in double-cut mode and chamfering on both ends
– Processing of tubes and rods –
Efficient production!
Peripheral Equipment and Accessories
Our production systems can be extended with numerous options to meet your specific requirements.
Here are some suggestions for you.
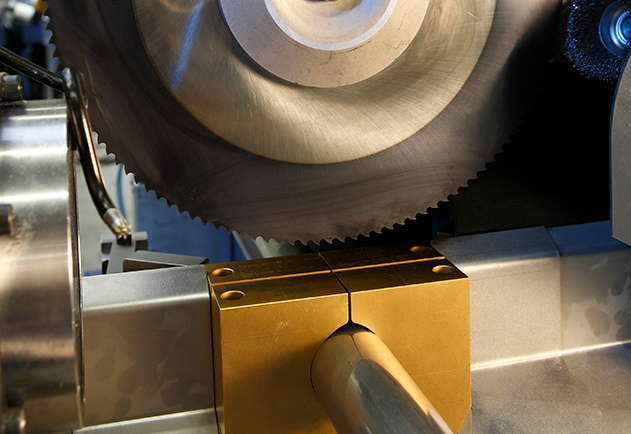
ACS® Production Systems for Sawing Tubes, Rods and Profiles
RATTUNDE sets global standards for reliability, productivity and quality. Precision electronics combined with proprietary software developed specifically for our systems guarantees accurate repeatability as well as minimal set-up and unit costs. Our machines produce outstanding results with thin-walled tubing as well. Extensive vertical integration and our own in-house research and development department enable us to influence practically all manufacturing processes to the fullest extent. That’s why we also equip our production systems with proprietary clamping and machining tools. Whether you want to process steel, stainless steel or non-ferrous metals, you’ll enjoy success with our equipment.
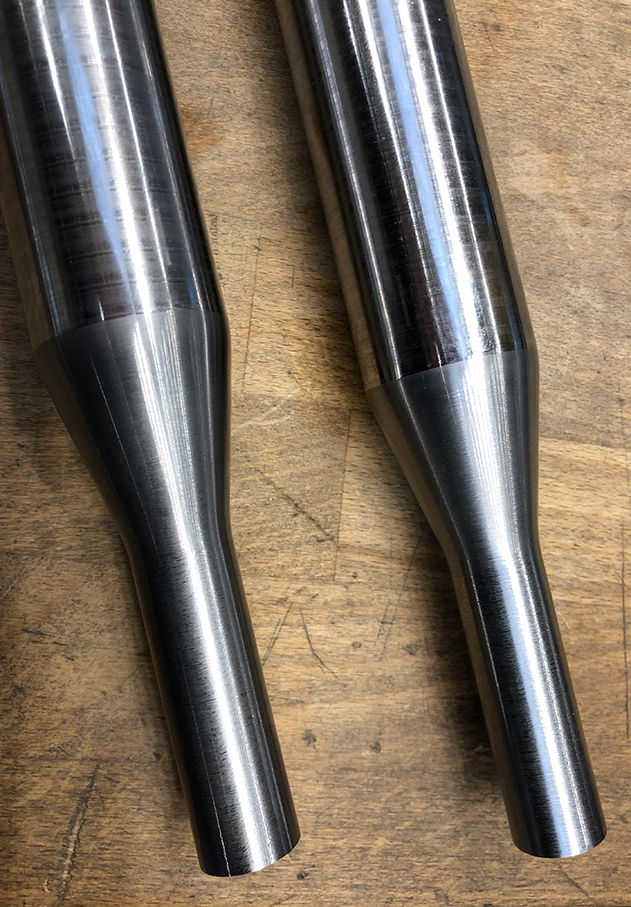
End-machining Tubes & Rods
RATTUNDE ACS® production systems automatically saw master lengths/fixed lengths into workpieces of any length and transfer these automatically to a subsequent machining process. The extensive range of machining options includes turning, chamfering and facing, thread cutting, drilling, profile turning, groove cutting, radius chamfering, angled chamfering and much more. Via minimal lubrication directly at the cutting edge of the tool, the system also enables you to achieve maximum quality and tool life when milling out the inside of a workpiece. User interfaces provide the operator with reliable guidance and ensure fast product set-up even with complex part geometry. The use of state-of-the-art machine control systems enables the seamless integration of every process in the machine design. For even greater process reliability in customer operations, we offer you extensive training for your operating and maintenance staff as well as product optimization. Comprehensive customer service around the globe completes our program.